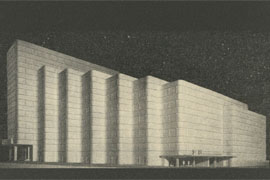
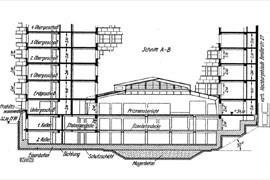
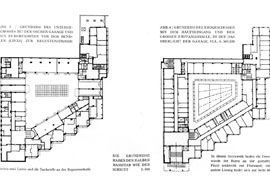
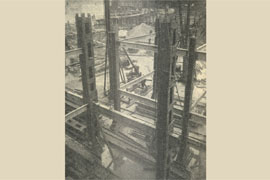
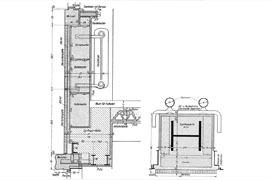
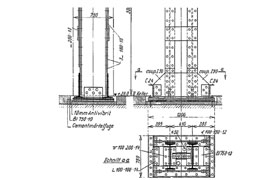
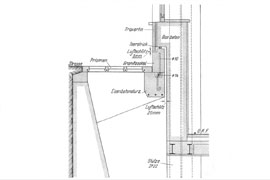
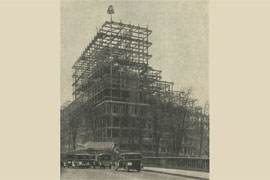
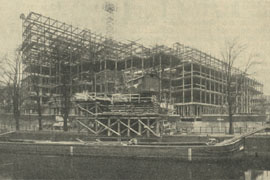
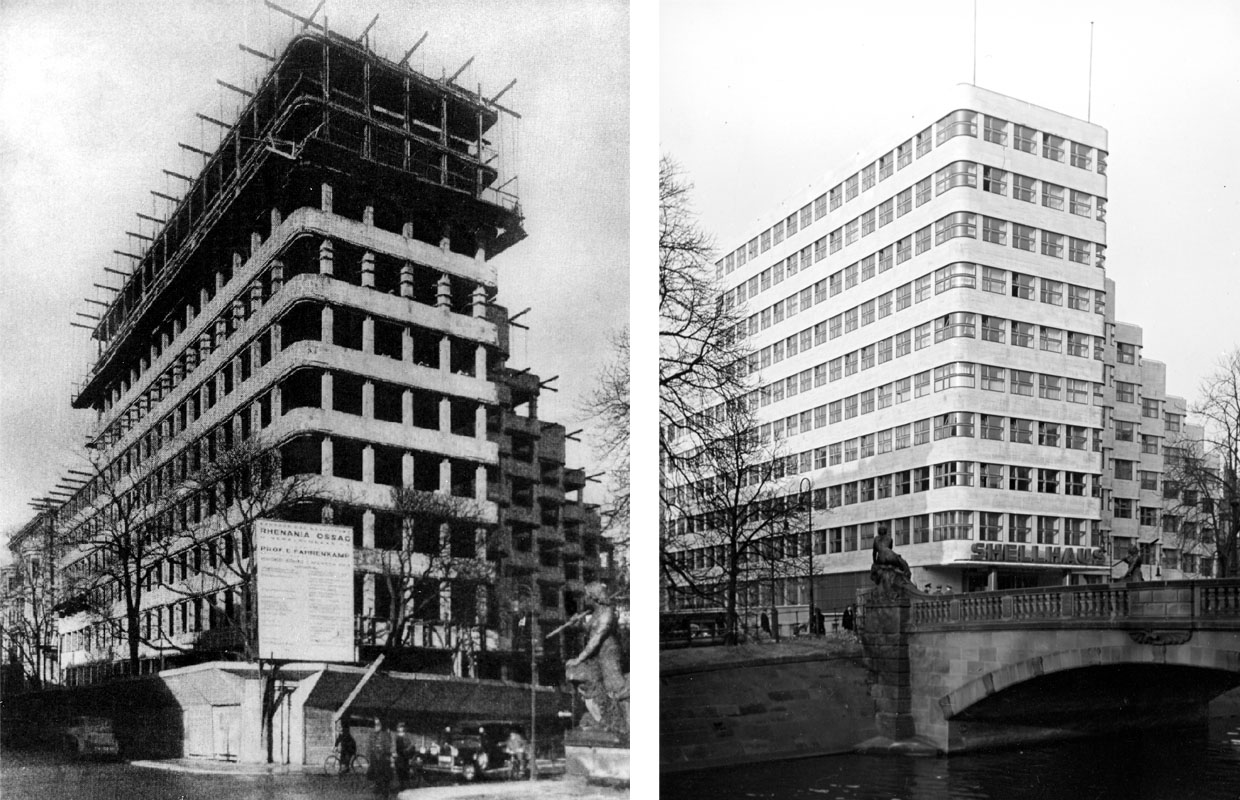
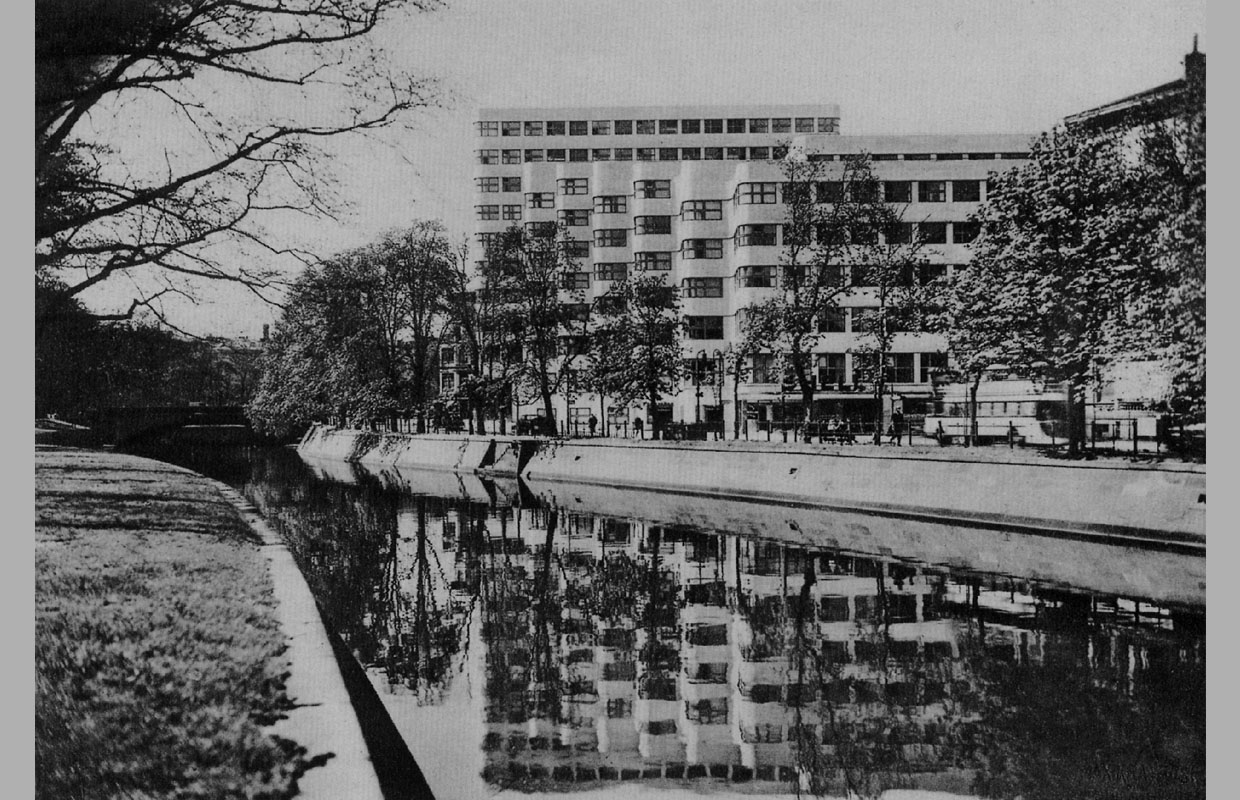
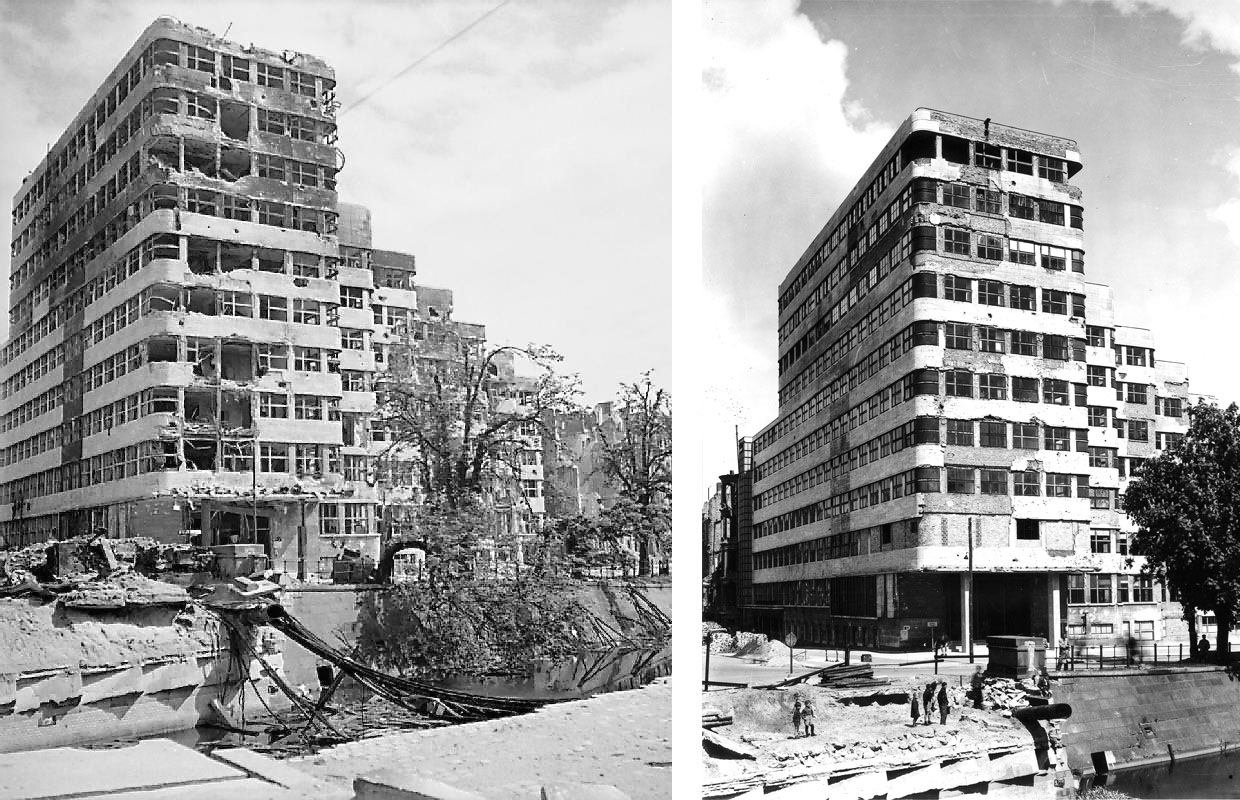
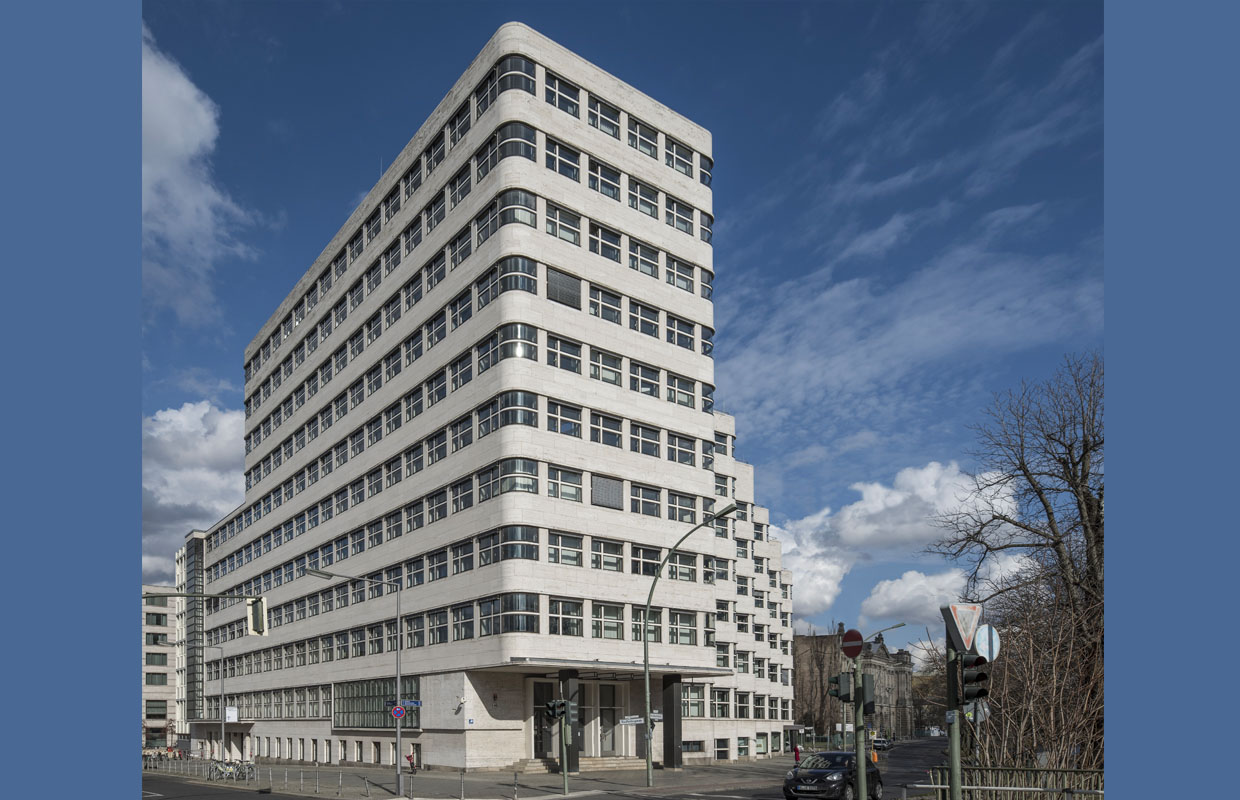
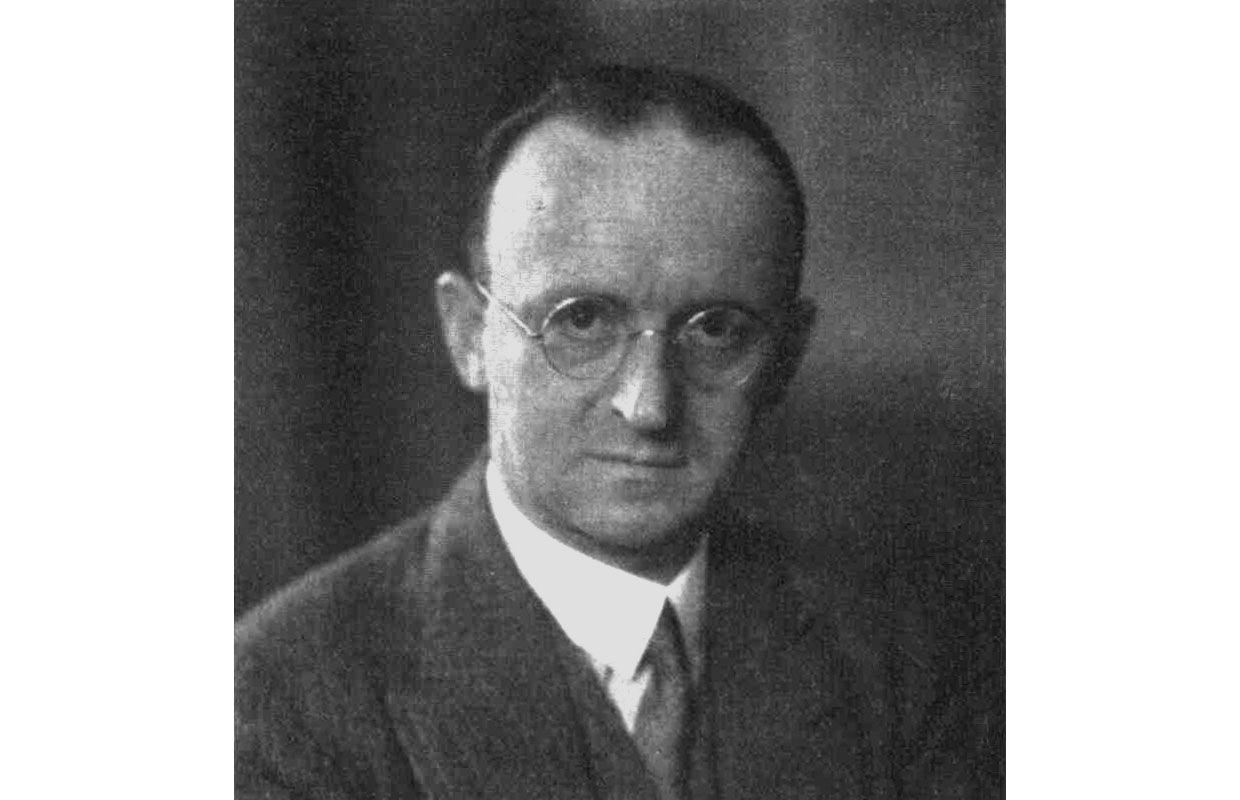
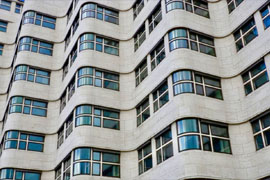
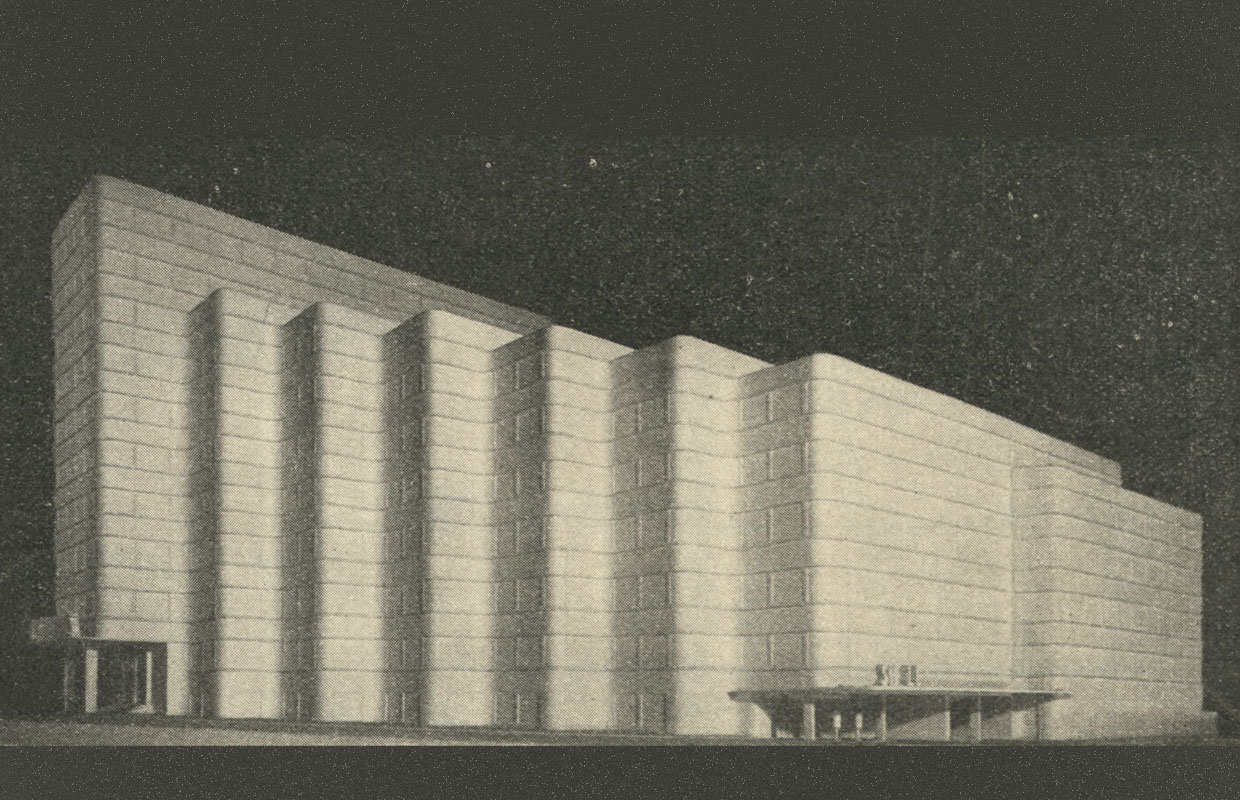
A trick enables one of Berlin's first high-rise buildings
In 1928, Rhenania-Ossag-Mineralölwerke AG, a subsidiary of the Dutch Shell Group, organised a competition for a new administration building in Berlin's Tiergarten district. The winner was the Düsseldorf architect Prof Emil Fahrenkamp (1885-1966).
With up to eleven storeys, the Shell building was one of the first high-rise buildings in Berlin. The characteristic staggered heights of the design are essentially a reaction to the requirements of the Berlin building regulations of the time, which still generally demanded compliance with the traditional "Berlin eaves height". The staggered height meant that this was clearly exceeded, but only in some areas.
Work on the foundation began in March 1930 and the building was completed two years later, at the beginning of 1932.
A trick enables one of Berlin's first high-rise buildings
In 1928, Rhenania-Ossag-Mineralölwerke AG, a subsidiary of the Dutch Shell Group, organised a competition for a new administration building in Berlin's Tiergarten district. The winner was the Düsseldorf architect Prof Emil Fahrenkamp (1885-1966).
With up to eleven storeys, the Shell building was one of the first high-rise buildings in Berlin. The characteristic staggered heights of the design are essentially a reaction to the requirements of the Berlin building regulations of the time, which still generally demanded compliance with the traditional "Berlin eaves height". The staggered height meant that this was clearly exceeded, but only in some areas.
Work on the foundation began in March 1930 and the building was completed two years later, at the beginning of 1932.
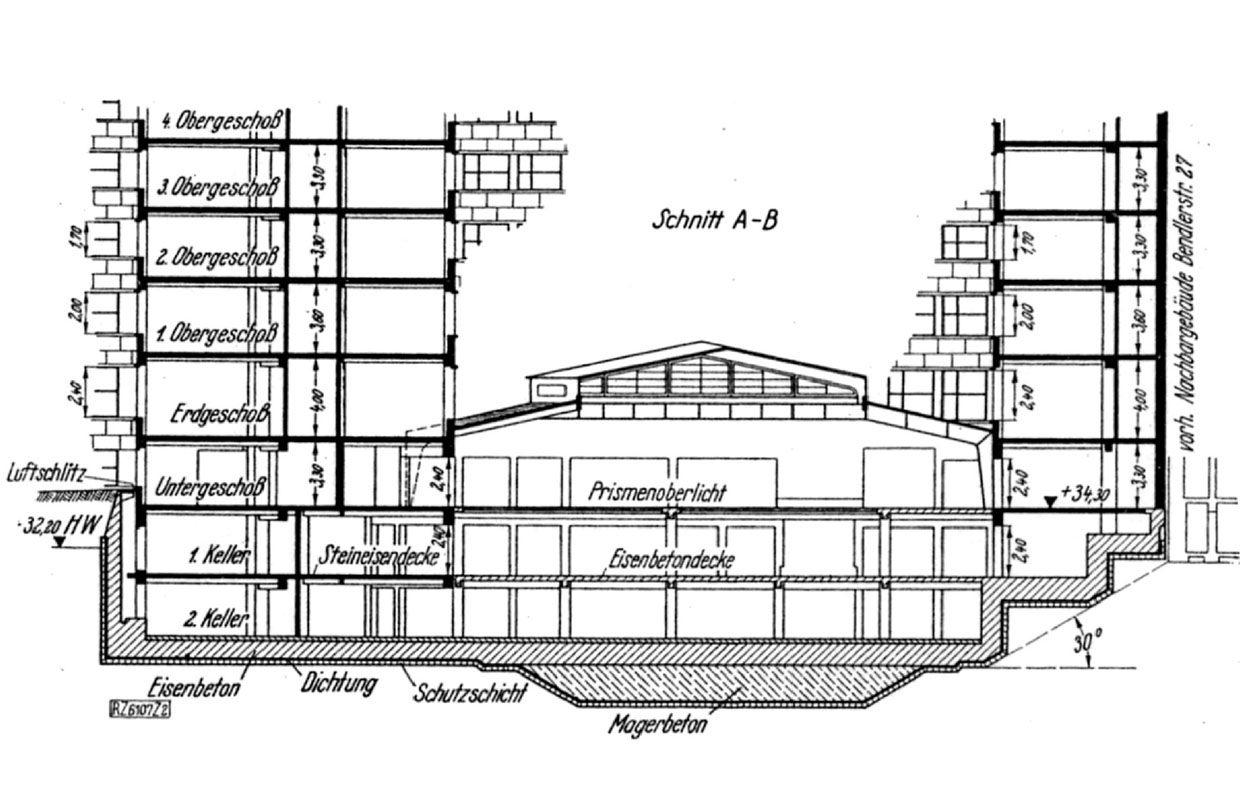
All in-house - underground car park and (Shell) petrol station
The cross-section (looking towards the tall corner building, Reichpietschufer on the left) shows the two basement levels, the upper of which was used as an underground car park. The basement above served as a (Shell) petrol station in the inner courtyard and was covered by a glass roof on a steel frame.
All in-house - underground car park and (Shell) petrol station
The cross-section (looking towards the tall corner building, Reichpietschufer on the left) shows the two basement levels, the upper of which was used as an underground car park. The basement above served as a (Shell) petrol station in the inner courtyard and was covered by a glass roof on a steel frame.
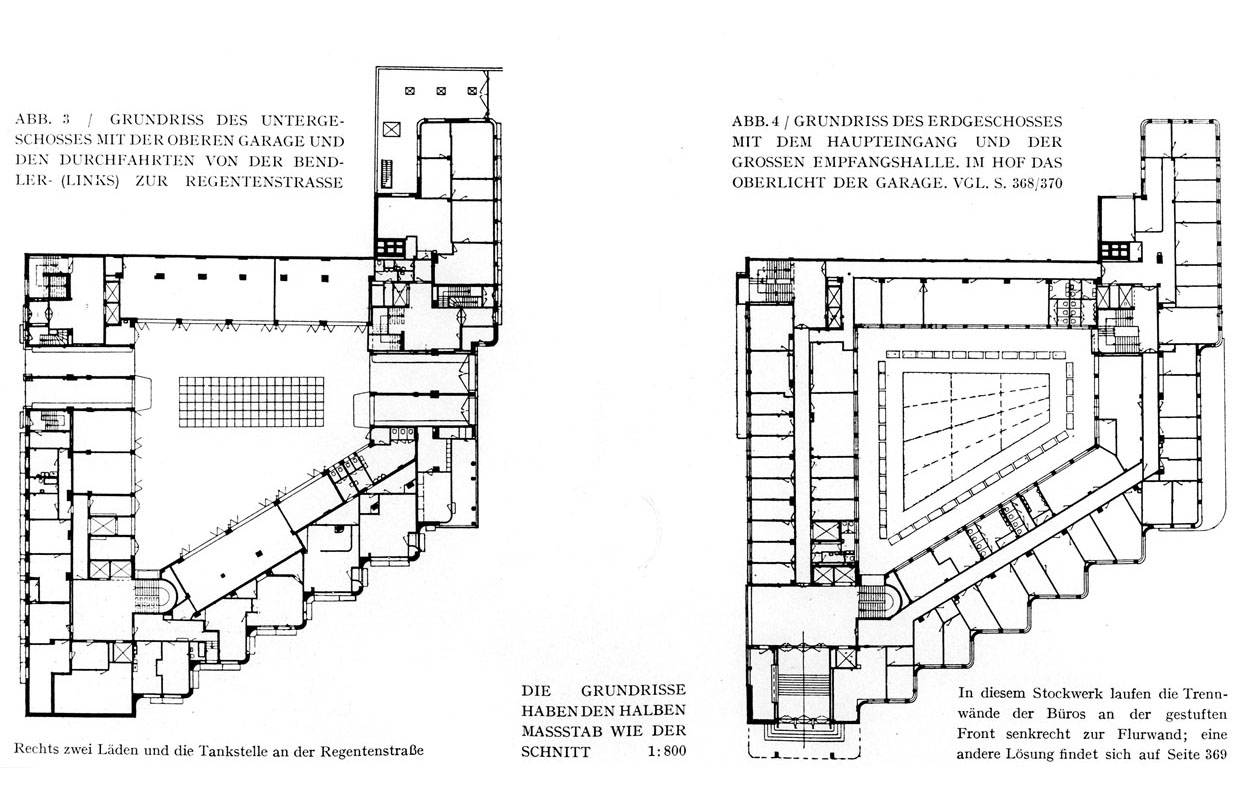
A real challenge for structural engineering
The trapezoidal floor plan with its façade recesses along the Landwehr Canal and the varying heights, as well as the requirement for traffic areas that were as free and flexible as possible without disruptive wall panels in the interior, presented the structural engineer Gerhard Mensch with major challenges.
A real challenge for structural engineering
The trapezoidal floor plan with its façade recesses along the Landwehr Canal and the varying heights, as well as the requirement for traffic areas that were as free and flexible as possible without disruptive wall panels in the interior, presented the structural engineer Gerhard Mensch with major challenges.
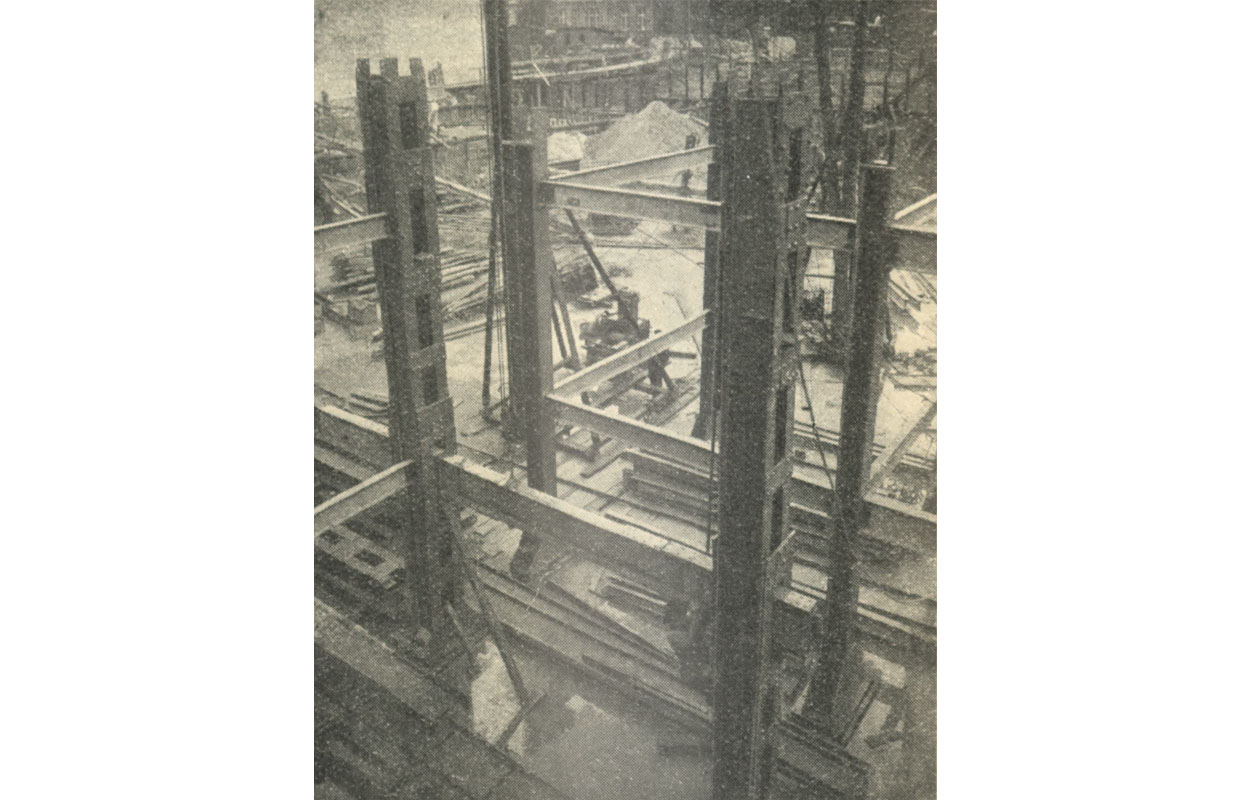
Riveted in prefabrication, screwed on the construction site
After comparative preliminary investigations, a steel frame construction was favoured. The structural elements composed of rolled sections, in particular the heavy frame columns and transoms, were prefabricated in the factory with riveted joints and simply bolted together on site. In the flatter areas, the columns had considerable load-bearing reserves, as they were generally designed for a possible later extension of all wings to 11 storeys.
The photograph shows the assembly of the frame columns on the foundation base in the winter of 1931/32.
Riveted in prefabrication, screwed on the construction site
After comparative preliminary investigations, a steel frame construction was favoured. The structural elements composed of rolled sections, in particular the heavy frame columns and transoms, were prefabricated in the factory with riveted joints and simply bolted together on site. In the flatter areas, the columns had considerable load-bearing reserves, as they were generally designed for a possible later extension of all wings to 11 storeys.
The photograph shows the assembly of the frame columns on the foundation base in the winter of 1931/32.
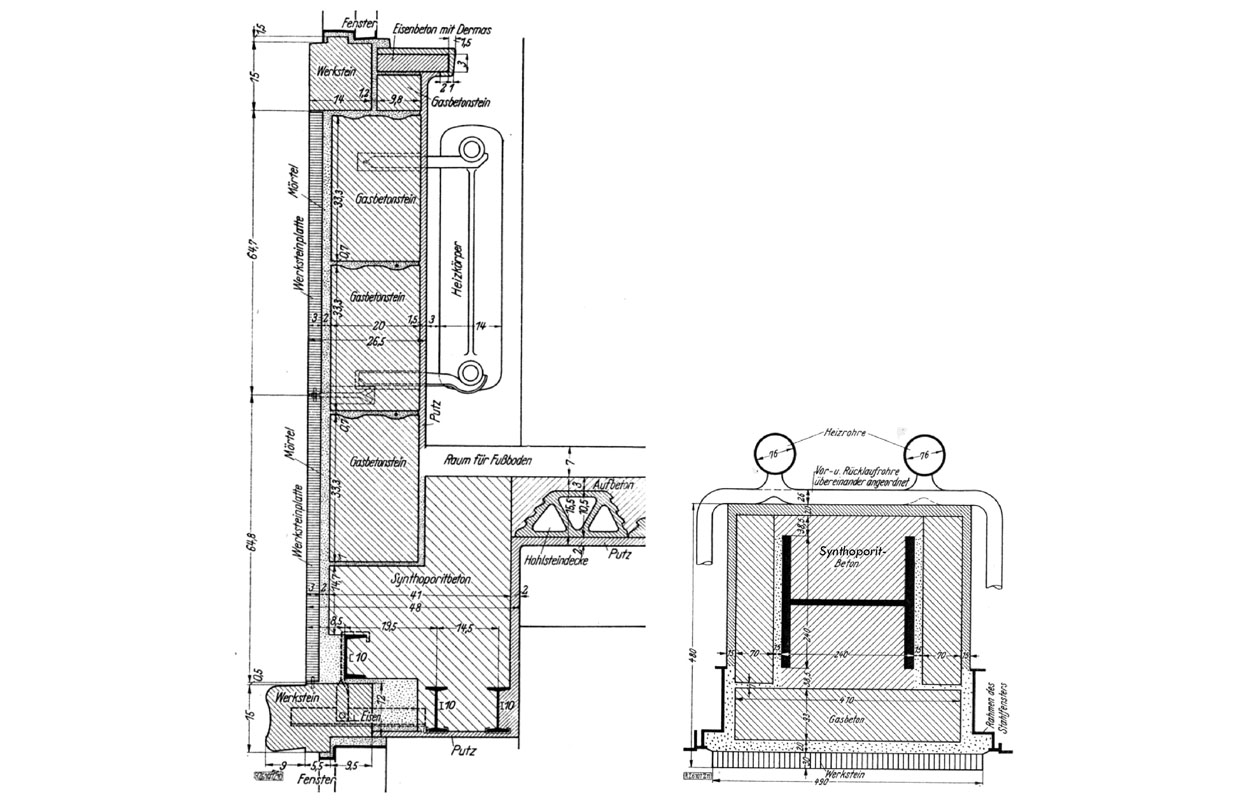
Fire protection, thermal insulation and high precision in detail
For fire safety reasons, all the columns were encased in aerated concrete blocks and then poured with "Synthoporitbeton", a lightweight aerated concrete. The porous materials chosen ensured a certain degree of thermal insulation - as did the "Aerokret" aerated concrete blocks from the company Torkret, which were used in the outer walls.
Later documentation of the sophisticated construction impressively emphasises the attention to detail with which the entire building was planned, right down to the precise representation of the radiators. The vertical section through a parapet (left) shows the original wall structure including an adjacent hollow ceiling block, while the horizontal section on the right shows the sheathing of the standard columns.
Fire protection, thermal insulation and high precision in detail
For fire safety reasons, all the columns were encased in aerated concrete blocks and then poured with "Synthoporitbeton", a lightweight aerated concrete. The porous materials chosen ensured a certain degree of thermal insulation - as did the "Aerokret" aerated concrete blocks from the company Torkret, which were used in the outer walls.
Later documentation of the sophisticated construction impressively emphasises the attention to detail with which the entire building was planned, right down to the precise representation of the radiators. The vertical section through a parapet (left) shows the original wall structure including an adjacent hollow ceiling block, while the horizontal section on the right shows the sheathing of the standard columns.
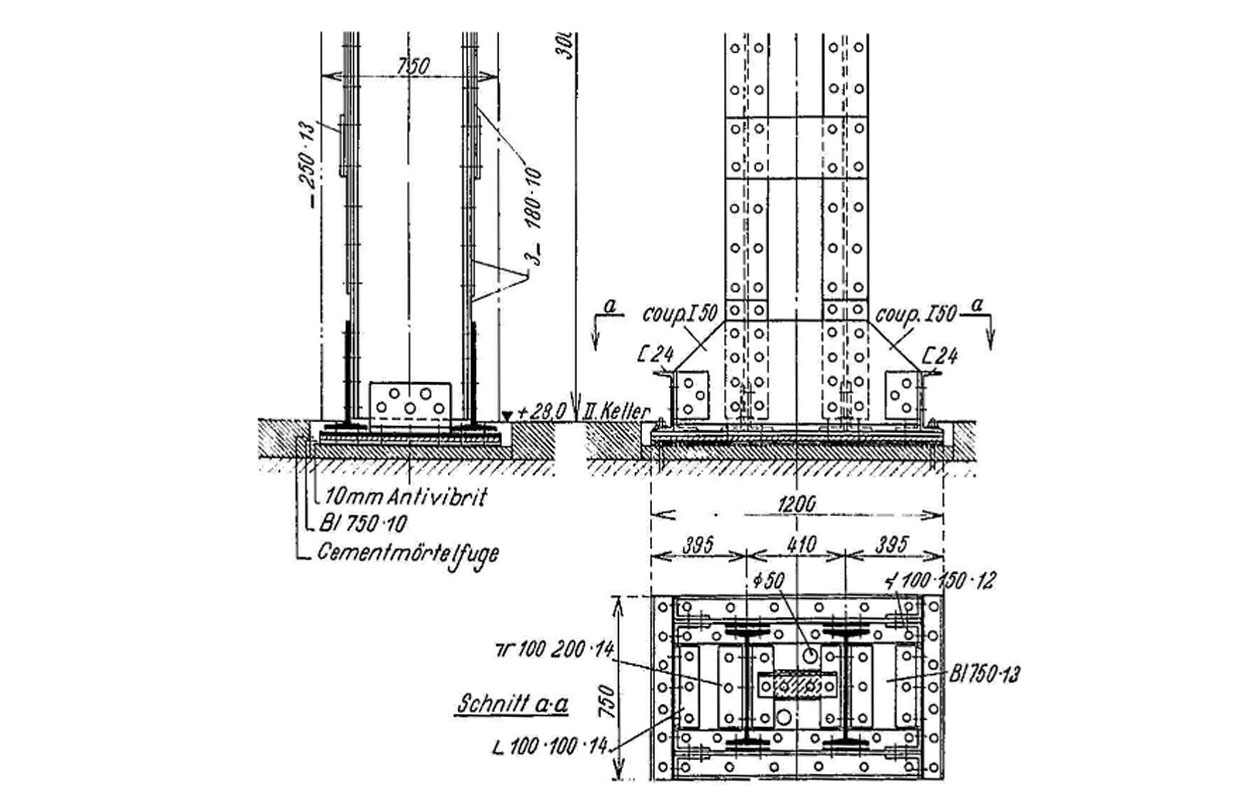
Steel structure and floor slab are vibration-decoupled
In order to minimise the transmission of vibrations from the busy riverside road to the steel structure, Gerhard Mensch developed special details for the vibration decoupling of the structure from its surroundings.
For example, 10 mm thick "Antivibrit" panels were inserted under all the steel columns to dampen any vibrations from the 1 metre thick reinforced concrete foundation slab.
Steel structure and floor slab are vibration-decoupled
In order to minimise the transmission of vibrations from the busy riverside road to the steel structure, Gerhard Mensch developed special details for the vibration decoupling of the structure from its surroundings.
For example, 10 mm thick "Antivibrit" panels were inserted under all the steel columns to dampen any vibrations from the 1 metre thick reinforced concrete foundation slab.
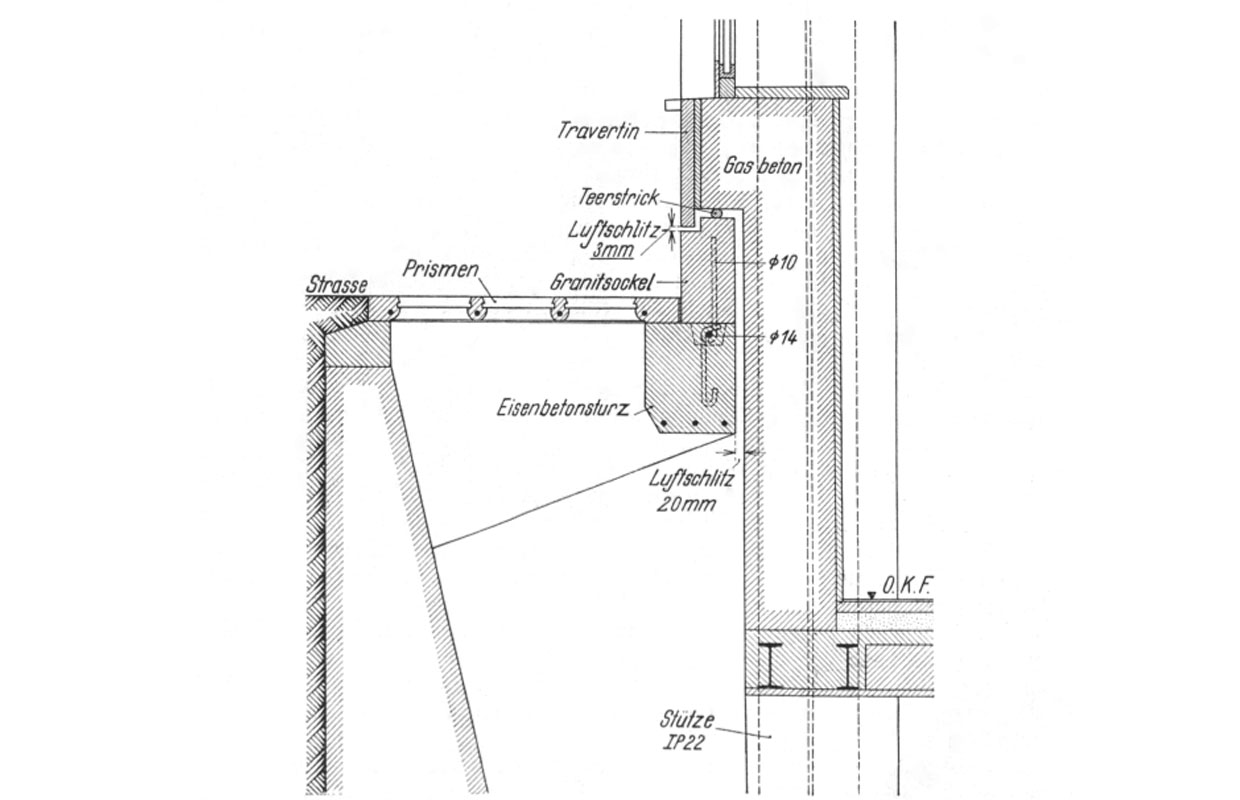
The skeleton also has no contact with the cellar walls
But there's more: the entire steel structure is also consistently separated from the reinforced concrete basement walls, which are clamped into the (possibly vibrating!) floor slab. A circumferential trench covered with glass blocks creates a gap between the steel structure and the reinforced concrete wall, and even in the transition to the wall of the rising storeys, a 3 cm wide air gap ensures consistent decoupling.
The skeleton also has no contact with the cellar walls
But there's more: the entire steel structure is also consistently separated from the reinforced concrete basement walls, which are clamped into the (possibly vibrating!) floor slab. A circumferential trench covered with glass blocks creates a gap between the steel structure and the reinforced concrete wall, and even in the transition to the wall of the rising storeys, a 3 cm wide air gap ensures consistent decoupling.
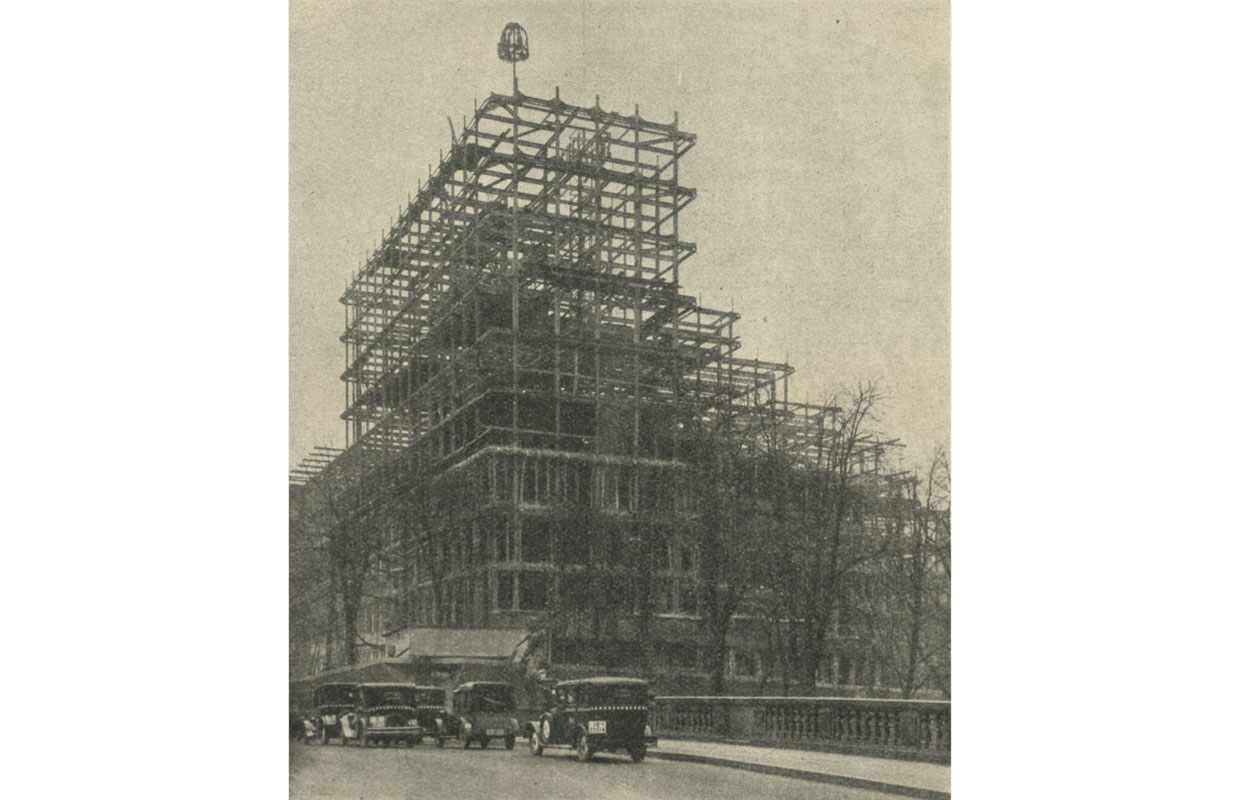
Topping-out ceremony after almost 4 months
The erection of the steel skeleton with a total weight of 2400 tonnes was completed on schedule in just 82 working days at the beginning of 1931.
The photograph shows the completed steel structure after the topping-out ceremony.
Topping-out ceremony after almost 4 months
The erection of the steel skeleton with a total weight of 2400 tonnes was completed on schedule in just 82 working days at the beginning of 1931.
The photograph shows the completed steel structure after the topping-out ceremony.
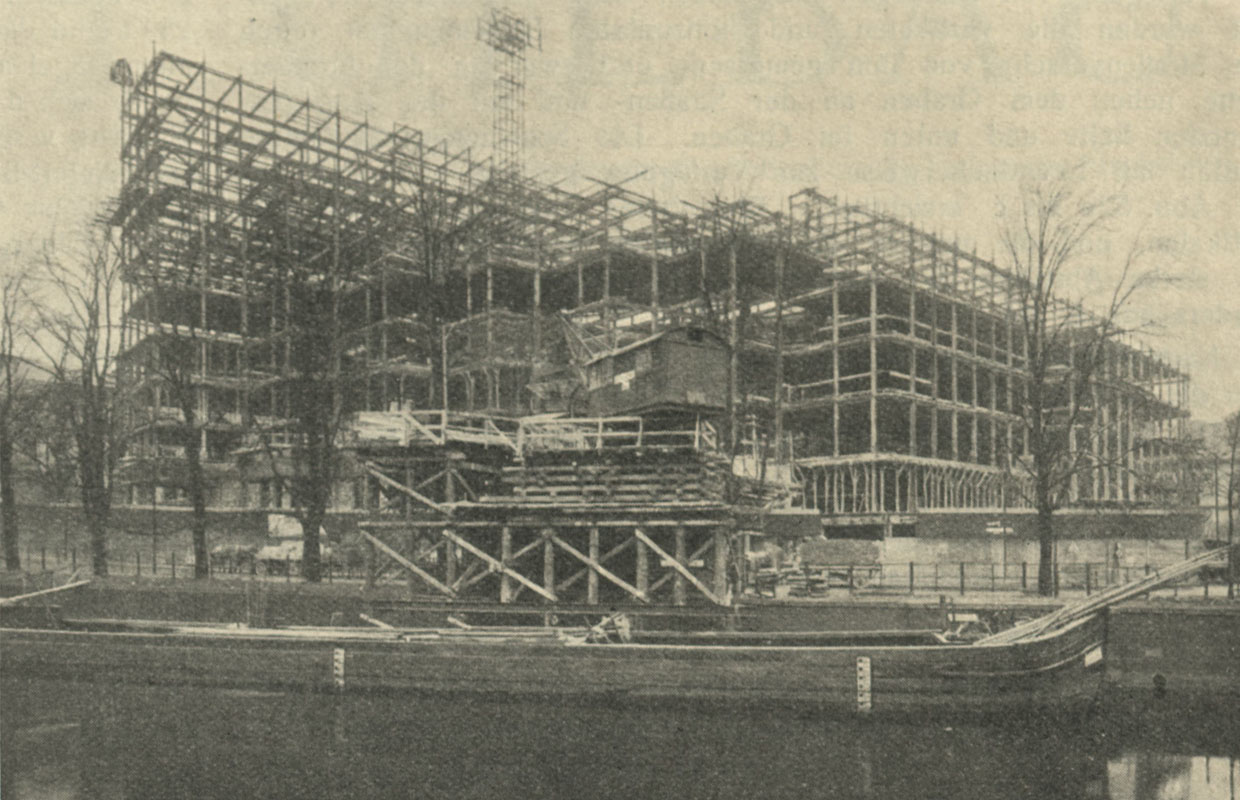
Building materials arrive via the Landwehr Canal
This photo was also taken after the topping-out ceremony, now from the opposite bank of the canal.
The heavy platform erected above the Reichpietschufer with the loading crane mounted on it is remarkable. Apparently, most of the material was delivered by ship via the Landwehr Canal.
Building materials arrive via the Landwehr Canal
This photo was also taken after the topping-out ceremony, now from the opposite bank of the canal.
The heavy platform erected above the Reichpietschufer with the loading crane mounted on it is remarkable. Apparently, most of the material was delivered by ship via the Landwehr Canal.
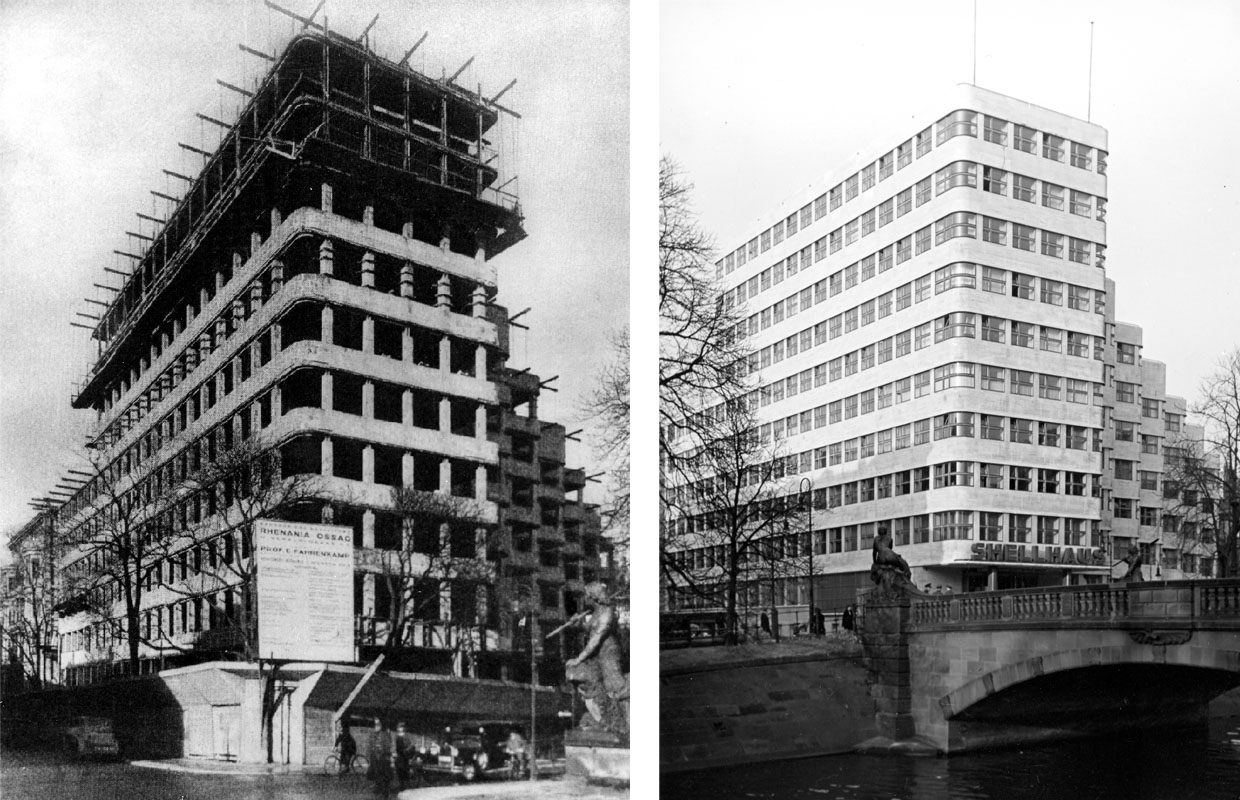
In 1932 the building is completed
In spring 1931, the parapets and column coatings were largely completed. In February 1932, the final building inspection took place. The Shell House was completed.
In 1932 the building is completed
In spring 1931, the parapets and column coatings were largely completed. In February 1932, the final building inspection took place. The Shell House was completed.
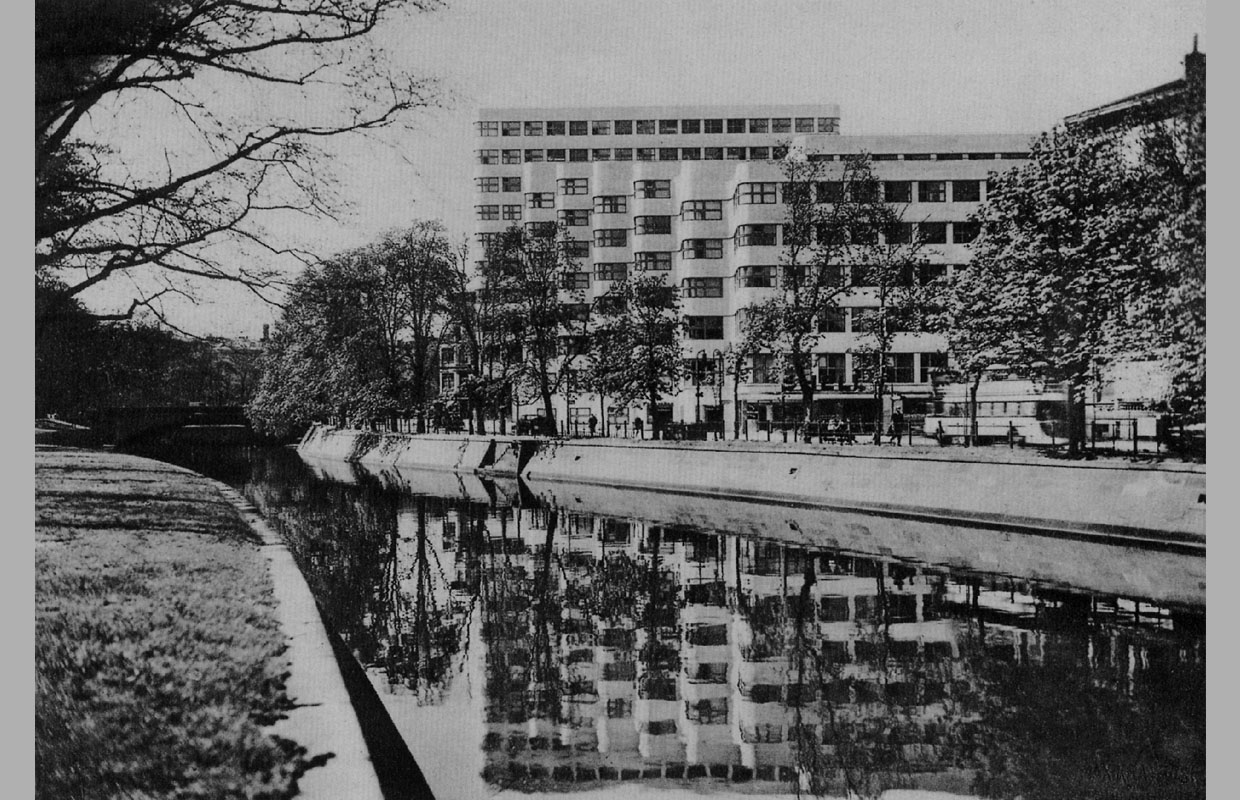
The Shell House - a "classic" of architectural Modernism
The photograph, probably taken in the summer of 1932, shows the staggered façade of the completed Shell Building and its reflection in the water of the Landwehr Canal in the view from the east. The fascinating perspective contributed to the Shell House soon becoming an icon of classical Modernism.
The Shell House - a "classic" of architectural Modernism
The photograph, probably taken in the summer of 1932, shows the staggered façade of the completed Shell Building and its reflection in the water of the Landwehr Canal in the view from the east. The fascinating perspective contributed to the Shell House soon becoming an icon of classical Modernism.
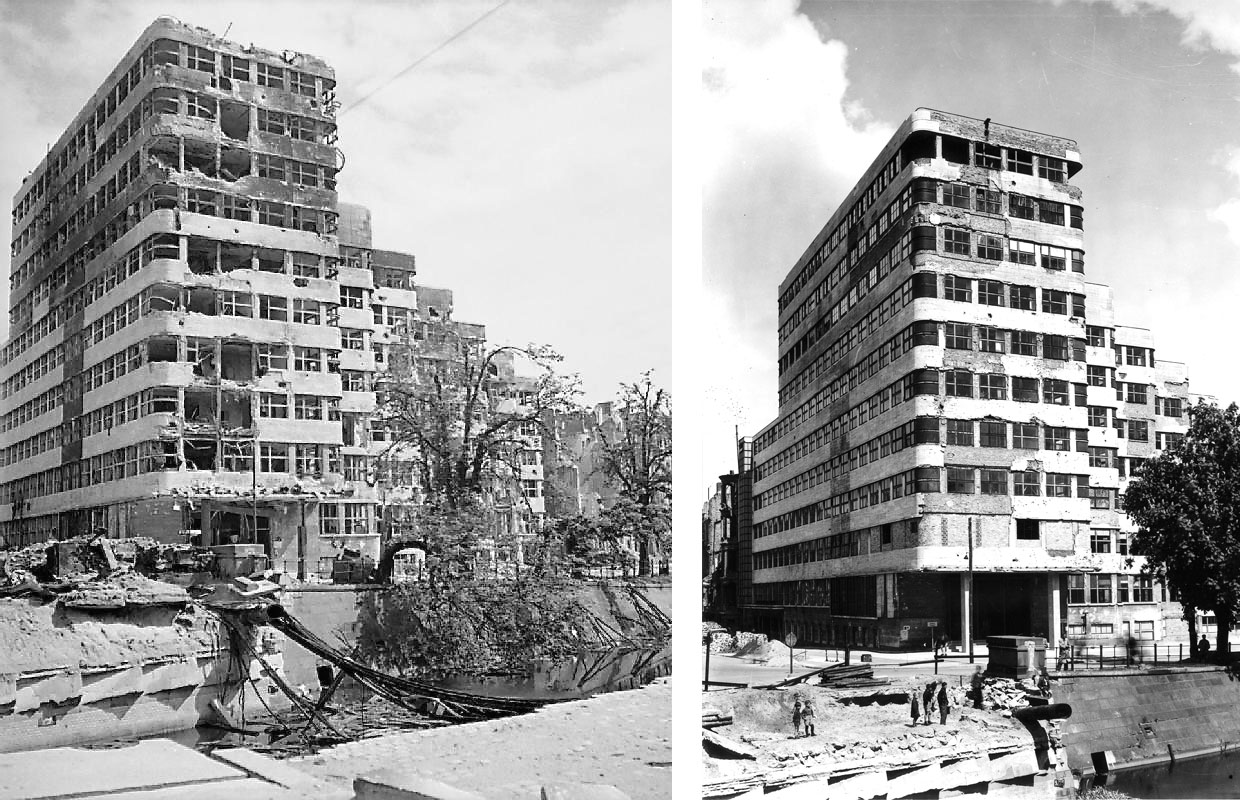
From 1947, the only moderate war damage is successively repaired
In 1939, the German Reich placed the Shell House - like other Western Allied properties - under trustee administration. In 1941, various offices of the High Command of the German Navy moved in, and a military hospital was established in the basement.
During the final battle for Berlin, there was considerable destruction, particularly to the façade facing the Landwehr Canal. Initial repairs began in 1947; damage to the steel structure was repaired and the gaps in the façade were closed using demolition bricks. From 1949, the Berliner Kraft- und Licht-AG (BEWAG) gradually moved into the building. In 1952, the removal of the war damage was completed.
The two photographs show the war-damaged building, on the left as a ruin, apparently in the summer of 1945, on the right already in use again on some floors, presumably in 1949. The gaps in the façade have been closed, the windows have already been reglazed in some areas.
From 1947, the only moderate war damage is successively repaired
In 1939, the German Reich placed the Shell House - like other Western Allied properties - under trustee administration. In 1941, various offices of the High Command of the German Navy moved in, and a military hospital was established in the basement.
During the final battle for Berlin, there was considerable destruction, particularly to the façade facing the Landwehr Canal. Initial repairs began in 1947; damage to the steel structure was repaired and the gaps in the façade were closed using demolition bricks. From 1949, the Berliner Kraft- und Licht-AG (BEWAG) gradually moved into the building. In 1952, the removal of the war damage was completed.
The two photographs show the war-damaged building, on the left as a ruin, apparently in the summer of 1945, on the right already in use again on some floors, presumably in 1949. The gaps in the façade have been closed, the windows have already been reglazed in some areas.
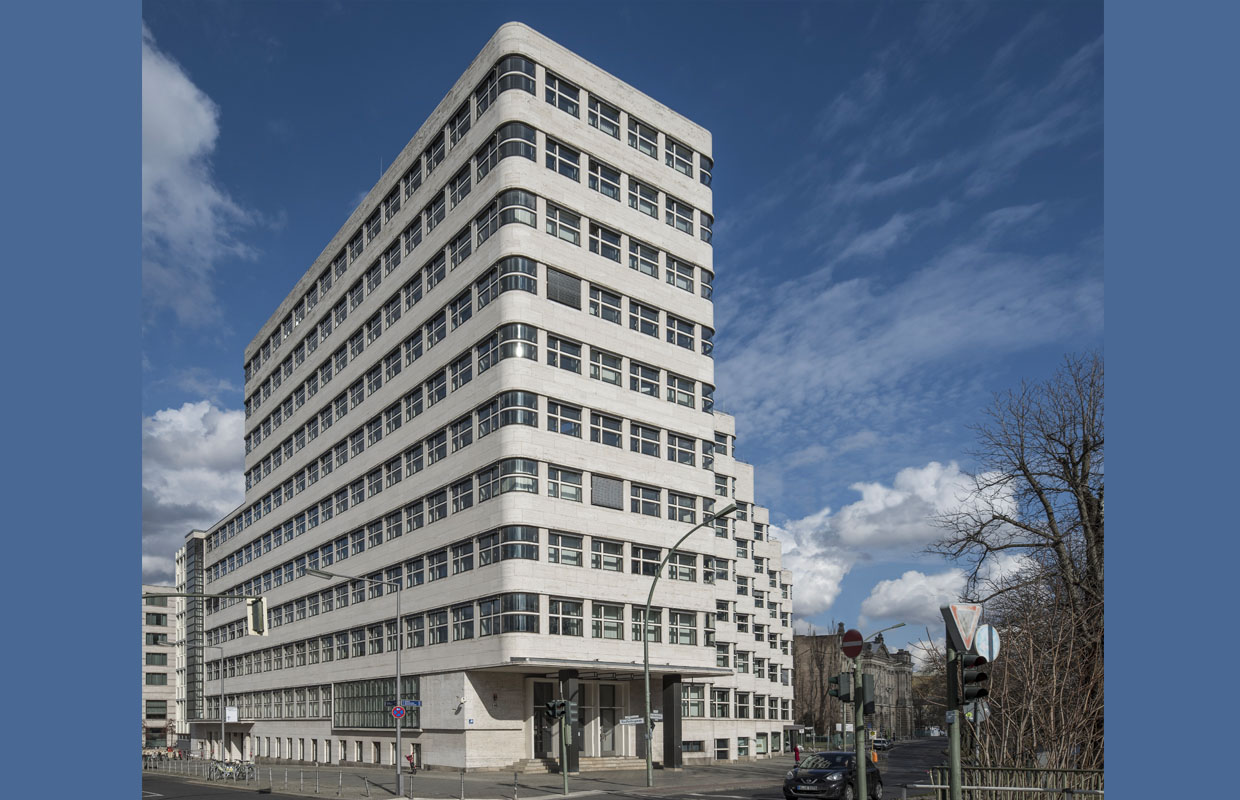
Today's façade is a new reconstruction
The current state of the building dates back to a basic renovation at the end of the 20th century. By 1984, cracks in the façade, corrosion and other damage had reached a level that made comprehensive refurbishment unavoidable. Accompanied by an almost unmanageable number of expert reports, this led to bitter disputes between BEWAG and the Berlin State Office for the Protection of Monuments over a viable refurbishment concept for the building, which had already been listed as a historical monument in 1958.
Restoration work finally began in 1998. When it developed into an outstanding pilot project in the still young field of modernist conservation. It was completed in summer 2000, the costs had risen to DM 80 million.
Nothing of the style-defining façade has been survived in its original state. However, the reconstruction was carried out with the utmost care and at great expense. To procure the 20,000 new travertine slabs, the already closed quarry at Tivoli near Rome was reopened, and the window frames, now made of bronze, corresponded even better than ever to Emil Fahrenkamp's ideas, who at the time had only been able to realise steel framed windows for cost reasons.
Today's façade is a new reconstruction
The current state of the building dates back to a basic renovation at the end of the 20th century. By 1984, cracks in the façade, corrosion and other damage had reached a level that made comprehensive refurbishment unavoidable. Accompanied by an almost unmanageable number of expert reports, this led to bitter disputes between BEWAG and the Berlin State Office for the Protection of Monuments over a viable refurbishment concept for the building, which had already been listed as a historical monument in 1958.
Restoration work finally began in 1998. When it developed into an outstanding pilot project in the still young field of modernist conservation. It was completed in summer 2000, the costs had risen to DM 80 million.
Nothing of the style-defining façade has been survived in its original state. However, the reconstruction was carried out with the utmost care and at great expense. To procure the 20,000 new travertine slabs, the already closed quarry at Tivoli near Rome was reopened, and the window frames, now made of bronze, corresponded even better than ever to Emil Fahrenkamp's ideas, who at the time had only been able to realise steel framed windows for cost reasons.
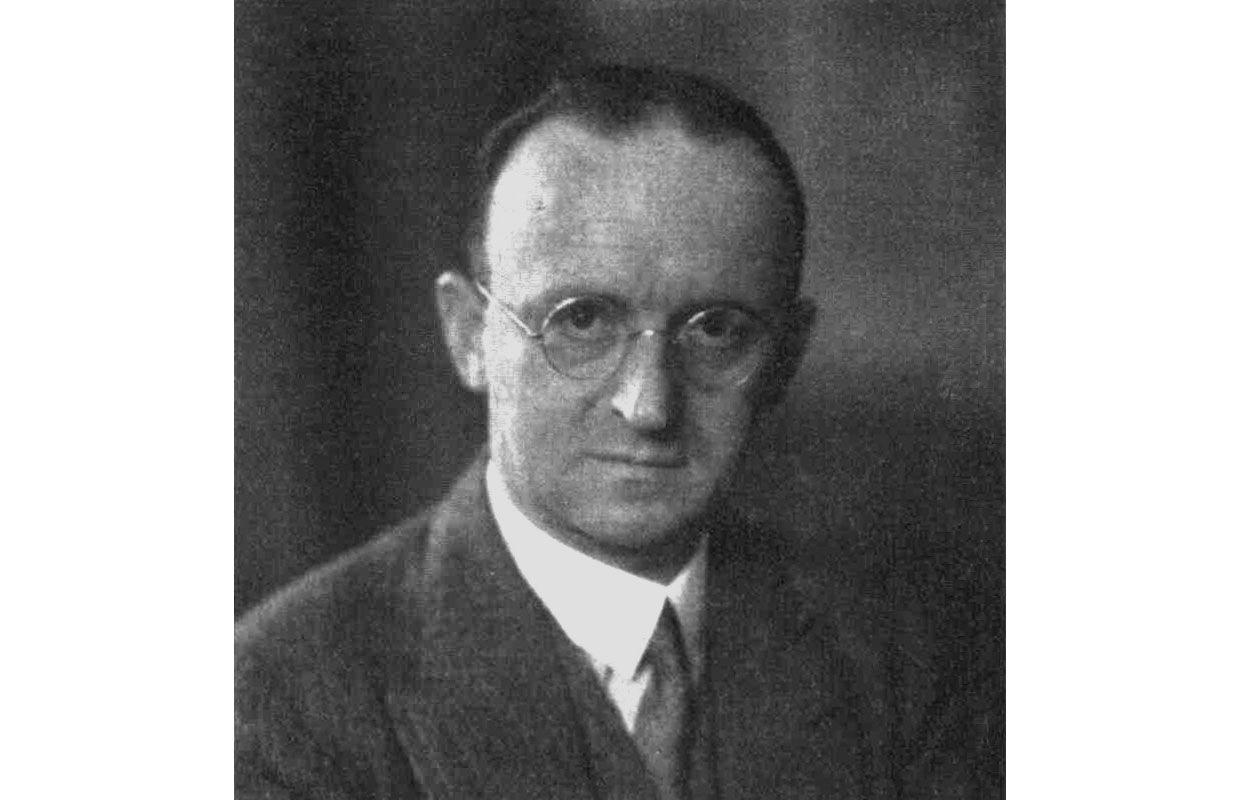
About the structural engineer
Gerhard Mensch (1880-1940), the engineer responsible for the construction of the Shell House, was one of the most important structural engineers of the first half of the 20th century in Berlin. After studying in the School of Engineering in Ilmenau (Thuringia) and gaining initial practical experience at Gutehoffnungshütte Sterkrade, he moved to Berlin in 1903. There he worked for many years in the office of the equally prominent structural engineer Karl Bernhard (1859-1937) before founding his own engineering office in 1921.
He was responsible for numerous prominent projects, particularly in the field of high-rise steel construction, starting in the 1920s with the wide-span halls of the depots of BVG (Berlin public transport company), through early high-rise buildings such as the Shell House and others for Siemens, to the new Reichsbank building (today's Foreign Ministry) and last not least Hitlers Neue Reichskanzlei at the end of the 1930s, for which he worked as inspection engineer.
About the structural engineer
Gerhard Mensch (1880-1940), the engineer responsible for the construction of the Shell House, was one of the most important structural engineers of the first half of the 20th century in Berlin. After studying in the School of Engineering in Ilmenau (Thuringia) and gaining initial practical experience at Gutehoffnungshütte Sterkrade, he moved to Berlin in 1903. There he worked for many years in the office of the equally prominent structural engineer Karl Bernhard (1859-1937) before founding his own engineering office in 1921.
He was responsible for numerous prominent projects, particularly in the field of high-rise steel construction, starting in the 1920s with the wide-span halls of the depots of BVG (Berlin public transport company), through early high-rise buildings such as the Shell House and others for Siemens, to the new Reichsbank building (today's Foreign Ministry) and last not least Hitlers Neue Reichskanzlei at the end of the 1930s, for which he worked as inspection engineer.
Key data
Location: Reichpietschufer 60–62, 10785 Berlin-Tiergarten
Construction period: 1930–32
Structural engineering: Gerhard Mensch
Overall planning: Emil Fahrenkamp
Realisation of construction work:
- Solid construction: Siemens-Bauunion, Wayss & Freitag
- Steel construction: Krupp-Druckenmüller, Breest & Co, Gesellschaft Harkort
- Aerated concrete walls: Deutsche Torkret-Baugesellschaft mbH
- Building façade: Philipp Holzmann
Key data
Location: Reichpietschufer 60–62, 10785 Berlin-Tiergarten
Construction period: 1930–32
Structural engineering: Bauingenieurbüro Gerhard Mensch
Design: Emil Fahrenkamp
Realisation:
- Solid construction: Siemens-Bauunion, Wayss & Freitag
- Steel construction: Krupp-Druckenmüller, Breest & Co, Gesellschaft Harkort
- Aerated concrete walls: Deutsche Torkret-Baugesellschaft mbH
- Building façade: Philipp Holzmann